LLC «NPP Elektrokontaktnye tekhnologii»
Induction heater of rollers (INV-1)
MAINTENANCE INSTRUCTION
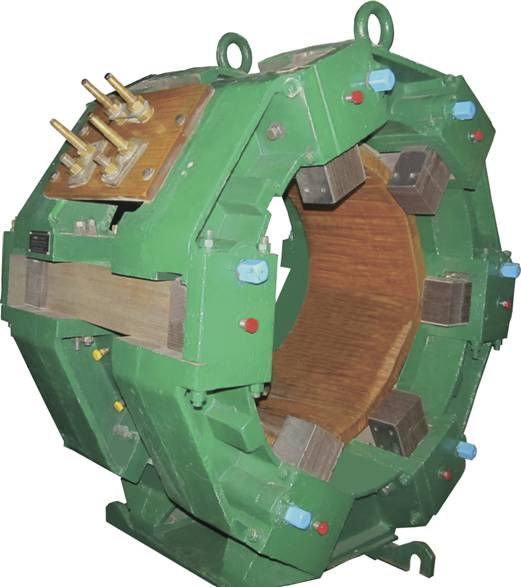
Induction heater of rollers (INV-1)
1. INTRODUCTION
The present maintenance instruction applies on an induction heater of rollers (INV-1) in diameter from 350 mm to 620 mm.
The maintenance instruction is the document explaining a design of an induction heater and its work, and also stating the main requirements to its installation and operation. The maintenance instruction is delivered to the customer with a product.
2. APPOINTMENT
2.1. The induction heater of rollers (INV-1) is intended for heating of rollers to temperatures 420°С – 450°С before a welding on at the stand and keeping this temperature in the course of a welding on roller on the rollerwelding machine until its complete recovery with the subsequent reuse in metallurgical production.
3. TECHNICAL CHARACTERISTICS
2.2. A working body – rollers with diameter from 350 to 620 mm
3.2. The temperature of heating of roller – 420 °C – 450°С
3.3. Heating time for rollers in diameter of 525 mm, 350 mm respectively – 2,0 hour, 1,5 hour
3.4. Voltage of an alternating current of industrial frequency – 380 V
3.5. Rated current – 250 A
3.6. Power factor – 0,607
3.7. Efficiency coefficient- 0,7
3.8. Value of capacity for compensation of reactive power – 1590 mkF
3.9. Class of electric isolation – N
3.10. Heater dimensions – 1315х1135х808 (mm)
3.11. Weight – 980Kg
3.12. A coolant – water from a water supply system
3.13. A consumption of water – 6,2 l/min
4. PRINCIPLE OF WORK OF THE HEATER AND ITS DESIGN
4.1.Principle of work of induction heater INV-1.
General view of induction heater INV-1 on fig. 1. As the induction heater is one of modifications of the single-phase transformer at which primary winding is the coil of excitement (1), a secondary winding – is roller, located in a free cavity in a heater. When voltage is giving on the coil there is a magnetic stream which partially passes through roller and induces in it currents which causes roller heating. The less stream is lost on dispersion the more effectively process occurs. To increase efficiency of heating, heater design provided with magnetic circuit with Movable poles which allow to bring closer a stream as it is possible to a roller. It is important, that poles were symmetrized against roller on a circle and were at identical distance from its surface. All other elements of a design are directed on realisation of a problem of increase of efficiency of heating without increase in consumption of capacity.
The case with built in it the coil of excitement (1), P-shaped magnetic circuit (2,4), mechanisms of adjustment of provision of poles (3,5,7,11), cooling system (fig. 2) and system of a supply of power supply (fig. 3) are included into structure of a heater.
4.2. Description of the heater design
4.2.1.The case of a heater is formed by two 6 section sides, connected among themselves by a rack which fastens to a floor or the cart. Siders are executed from alumium-cast moulding.
4.2.2.Each section contains P-shaped magnetic circuit with the Fixed core (4) and two Movable poles (2). Magnetic circuit represents a set of thin plates (average 0,5 mm) transformer steel with the isolated surface. The set placed between two press flanges and pulled together with rivets. Magnetic circuit is formed by a package of the Fixed core and two packages of poles. As a result of the repair packages of poles were completely renewed. Need of updating was connected with that when dismantling magnetic system of tin poles appeared completely short-circuited. The short-circuited poles can be one of the reasons of decrease in efficiency of heating the roller when using this device. The tins appeared as a result of dismantling of poles were subjected to removal of agnails on machine, heating off magnetic properties, to covering with an insulating cover on their surface with the subsequent heat treatment in the furnace at temperature 200°С. As a covering varnish КО916 and P5 solvent was used.
To avoid deformation of poles, the thickness of new press flanges is increased to 6,0мм. Packages are pulled together with the steel rivets previously isolated by a glass tape, impregnated with varnish КО916. Sizes of new poles: 270х119х80 (mm).
The Fixed cores which were in a good condition, are fixed to side walls of the corresponding sections and provide additional rigidity to the case in the axial direction. Sections sidewalls on a circle are connected by themselves by pins through insulating laying. Joints of sections creates nests in which Movable poles (2) are placed.
4.2.3.The mechanism of regulation of position should provide fixing of position of a pole, moving of a pole and restriction of limits of moving of a pole.
The movement of a pole fixes a bolt (6). On a heater it is painted by dark blue colour.
Rack transmission is used for moving of a pole which will transform a rotary motion to the translational. In a nest the shaft gear with a tetrahedral bolt (5) on an exit (it is painted in red colour) for a wrench operation. The lath (3) is positioned on a press flange of a pole. In the presence of gearing, having released fixing bolt (6), it is possible, turning a bolt (5), to change smoothly the position of a pole within 140 mm. In the press flange (11) being on the opposite side of a flange (3), the cut is made into which the bolt (7) with a lock-nut (9) comes and draws in a lath to a gear that provides reliable gearing of a gear with a lath within a pole course. Cut limits the way of moving of a pole. The shaft gear (5), the bolt fixing the provision of poles (6), bolt clamping (7) with a nut (9), press flanges of poles with a lath (3) and cut (11) form the mechanism of adjustment of provision of poles.
4.2.4. The coil (1) positioned in a lodgment on an internal surface of the case. Its position on a circle and along an axis is aligned through laying by the adjusting bolts (8) painted in yellow colour..
The cylindrical coil, is made from hollow copper soft tube D14х2 mm in which circulates water. The coil consists of two semi-coils (left and right) with equal number of rounds-35. Each semi-coil is reeled up in three layers with distribution of rounds on layers respectively 12, 11, 12 and has two endings (the beginning and the end). Marking of endings: 1.1., 1.2. – the beginning and the end of the left semi-coil; 2.1., 2.2. – beginning and end of the right semi-coil. Semi-coils are carefully isolated by heat resisitant materials on the basis of isinglass-stone (more detailed the design of isolation is described in the passport), class H Isolation.
As case isolation used glass fiber STEF-1 with the thickness 1,0мм from which two cylinders on external and internal diameter of the coil are executed, covering both semi-coil, structurally uniting them in a whole. At the same time these cylinders serve as protection against mechanical damages. All this design is covered with a glass tape, the endings are welded with connectors (fig. 2), and in such look the coil goes on impregnation. The coil becomes impregnated with varnish КО916К and is exposed to heat treatment within the 16 hour at temperature 160°С. The coil is established in the heater case. The terminal board fastens to the sides. The connectors are placed on a terminal board and fasten with bolts.
Busbars which provide consecutive electric connection of semi-coils are connected to connectors. Power feeds on plugs 1.1., 2.2., plugs 1.2. and 2.1. are short-circuited by the busbar (fig. 3). The coil has external diameter of 750 mm, internal – 640 mm, length in the axial direction of-400 mm. Mass of the coil is 140 kg.
Cooling system. Hydraulically semi-coils connected in parallel that illustrates fig. 4. Connectors 21., 2.1, having identical electric potential, are connected by the general collector working in the field of an elevated pressure, and through the connectors 1.1., 2.2., exposed to the power, it is carried out water plums. On fig. 2 the drawing of the connector, which welded to a copper tube by PSR25 solder for a water supply to the coil, forming the beginning and the end of each semi-coil is given. The supply of water should be carried out by rubber hoses. Cooling of a copper tube have to be done with clear water, without extraneous impurity with pressure to the 4th atmospheres, use of drinking water from a water supply system is allowed also. By calculation in a nominal mode the consumption of water of 6,2 l/mines provides its overheat on 40°С.
Power supply system. The heater can directly be connected in a network if the input cable is ready on 300А. But considering low power factor, it is recommended for compensation of the jet capacity consumed by a heater, to connect in parallel to main unit the battery of condensers in capacity 1590 мкФ according to the scheme provided on fig. 5. In the process of heating of roller it is desirable to carry out periodic measurements by pincers of currents in a input cable, a condenser chain and a loading chain for comparison of calculation to experiment.
5.INSTALLATION AND HEATER WORK
The following order of installation and heater work is recommended:
5.1. To establish a heater on a workplace, previously released it from the elements necessary at transportation of such, as extensions of the coil, bolts in openings of connectors. To carry out visual survey.
5.2. To measure level of isolation of the coil to the case with mOhmmeter – 500V.
5.3. To ground a heater.
5.4. To bring power supply to bolts 1.1, 2.2 on a terminal board.
5.5. To bring water to connectors according to the scheme fig. 4.
5.6. To carry out visual survey of the condenser battery, to wipe contact surfaces, to check places of connections with a cable and operability of switching equipment.
5.7. To switch poles (12 units) in extreme top situation. In particular,
5.7.1. To release fixing bolt (6) (dark blue),
5.7.2. Smooth turn of a bolt (5) (red) to regulate the position of a pole,
5.7.3. The new position of a pole to fix with a bolt (6),
Attention! Within length of rack gear that corresponds to length of moving of a pole of 140 mm, do not to touch a bolt (7)!
5.7.4. Operation (pct 5.7.1-5.7.3.) to extend on all 12 poles.
5.8. To insert roller into a space of a heater
5.9. To bring poles to a surface of roller with a uniform gap, having repeated operations pt 5.7.1., 5.7.2., 5.7.3.
Size of a gap should be optimum taking into account time of heating and quality of the surface received as a result of heating. The optimum gap is defined experimentally. A recommended gap of 5-50 (mm).
5.10. To feed the coil with water.
5.11. To feed the power on the coil, consistently connecting batteries of condensers according to the scheme 5.
6.THE RECOMMENDED MODE OF HEATING OF THE ROLLER.
6.1 For uniform warming up of a surface of the roller and in order to avoid formation of cracks on its surface it is recommended to disconnect 3-4 times a heater from a power supply for 5-7 minutes.
6.2. To disconnect the power supply you have to follow the inverted order, i.e. in the beginning disconnect condenser batteries, and then a heater.
6.3. The roller heats up to temperature 420°С.
7. RULES OF USAGE, PROVIDES MAXIMUM EFFICIENCY AND DURABILITY OF THE INDUCTION HEATER
7.1. It is strictly forbidden to expose power to a heater in absence the roller in a heater cavity. Because of sharp falling of inductive resistance power giving in this case can cause inadmissible growth of a current, increase in temperature of cooling water up to boiling and to failure of the coil of a heater.
7.2. To watch that poles positioned against surface of the roller with an identical gap. It will lead to reduction of a magnetic stream of dispersion, to increase in interaction of the main current with the currents induced in the roller, and to increase of efficiency of heating.
7.3. To watch rail coupling of poles with the case. Not to beat a sledge hammer or other heavy subject on poles, for their moving. When the provision of a pole needs to be displaced on distance smaller, than 140 mm, it is necessary to use rail gear according to pct 5.7.1., 5.7.2., 5.7.3. present instruction.
7.4. If the course of a pole has to exceed 140 mm, it is necessary to untwist bolts (7) and (6) (dark blue), accurately manually to deduce a pole from gearing, to pose it in the necessary position and to fix bolts (6) and (7). It is desirable, that this operation was carried out by the qualified serviceman.
8. INDICATION OF SECURITY MEASURES
8.1. Operation, service and repair of the inductor is authorised to the persons, who had preliminary training preparation and familiarised with this instruction.
8.2. At operation, service and repair of an electrotechnical part of a heater it is necessary to be guided by «User Rules for Operating Electrical Equipment» and «User Safety Rules for Operating Electrical Equipment to 1000 V».
8.3. Control and check of a heater to make not less, than two persons.
8.4. It is forbidden to include a heater with loose poles and not grounded case.
8.5. It is forbidden to make adjustment in heater operating time.
8.6. At operation of a hydraulic part it is necessary to be guided byrequirements for safety measures for hydraulic units.
9. MAINTENANCE
The personnel serving induction heating installations, is obliged to conduct systematically supervision over the heating of constructive elements induced currents of electromagnetic fields of dispersion. Depending on the received results should be taken measures for decrease in losses of the electric power. Installation should be kept clean. Rubbing of installation elements from a production dust have to be made periodically depending on working conditions, but is not rare than once a month. Installation should be served by electrical engineers on duty. The personnel which is directly serving electroinduction installation, should pass annually training and examination of rules of technical operation and safety.
10. CARE OF THE HEATER
Periodic surveys and scheduled preventive maintenance should be carried out according to the schedule approved by the chief power engineer of the enterprise. Survey is made by the personnel on duty. Results of survey and the taken measures for elimination of malfunctions are registered in log. At surveys the special attention should focused on:
-reliability of grounding;
-lack of a scum on water cooled surfaces;
-lack of a dust on parts of installation.
Survey and repair work are made at disconnection of a heater from the power supply.
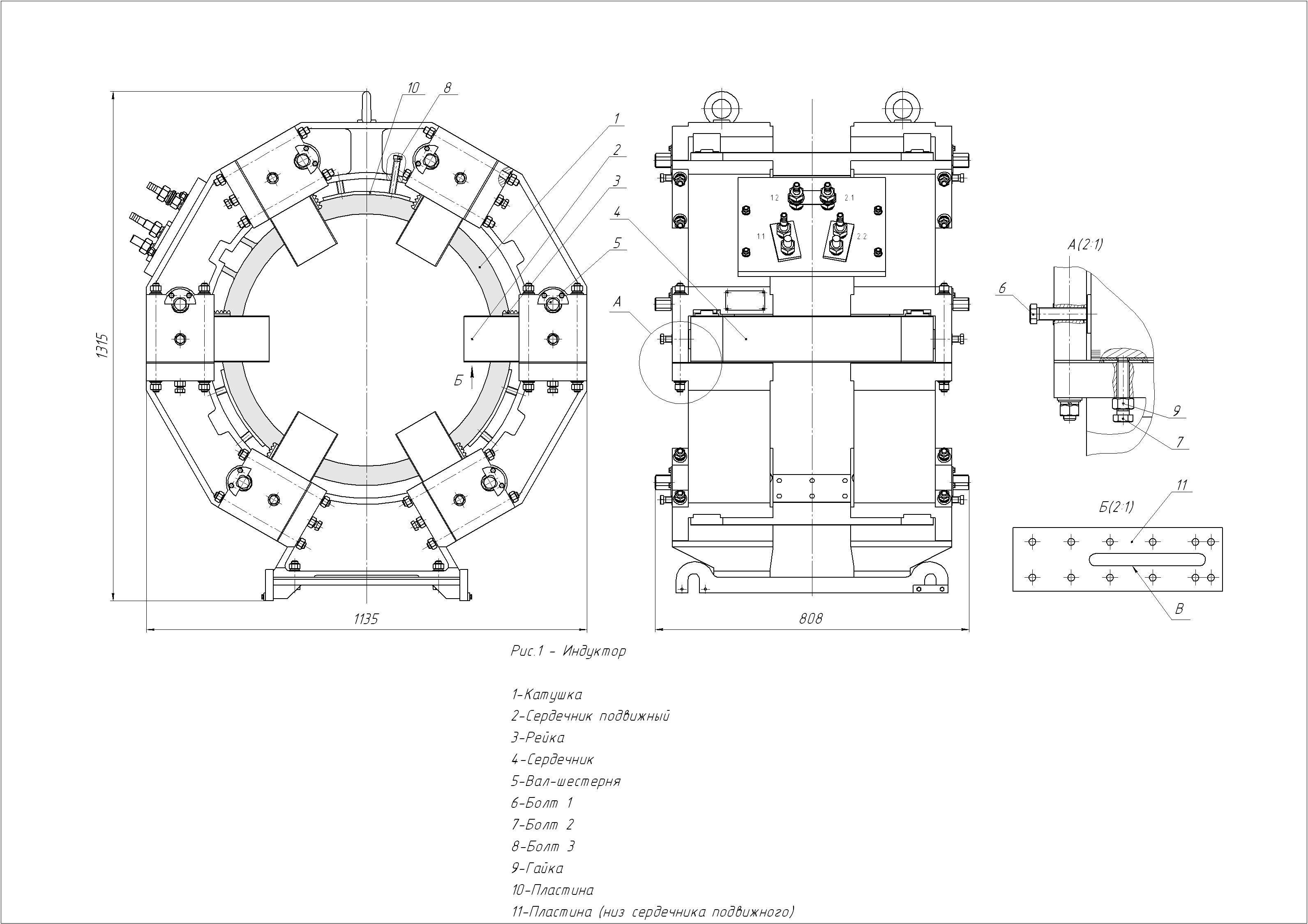
Induction heater of rollers (INV-1)